The Worlds Smallest Sheet Film Camera
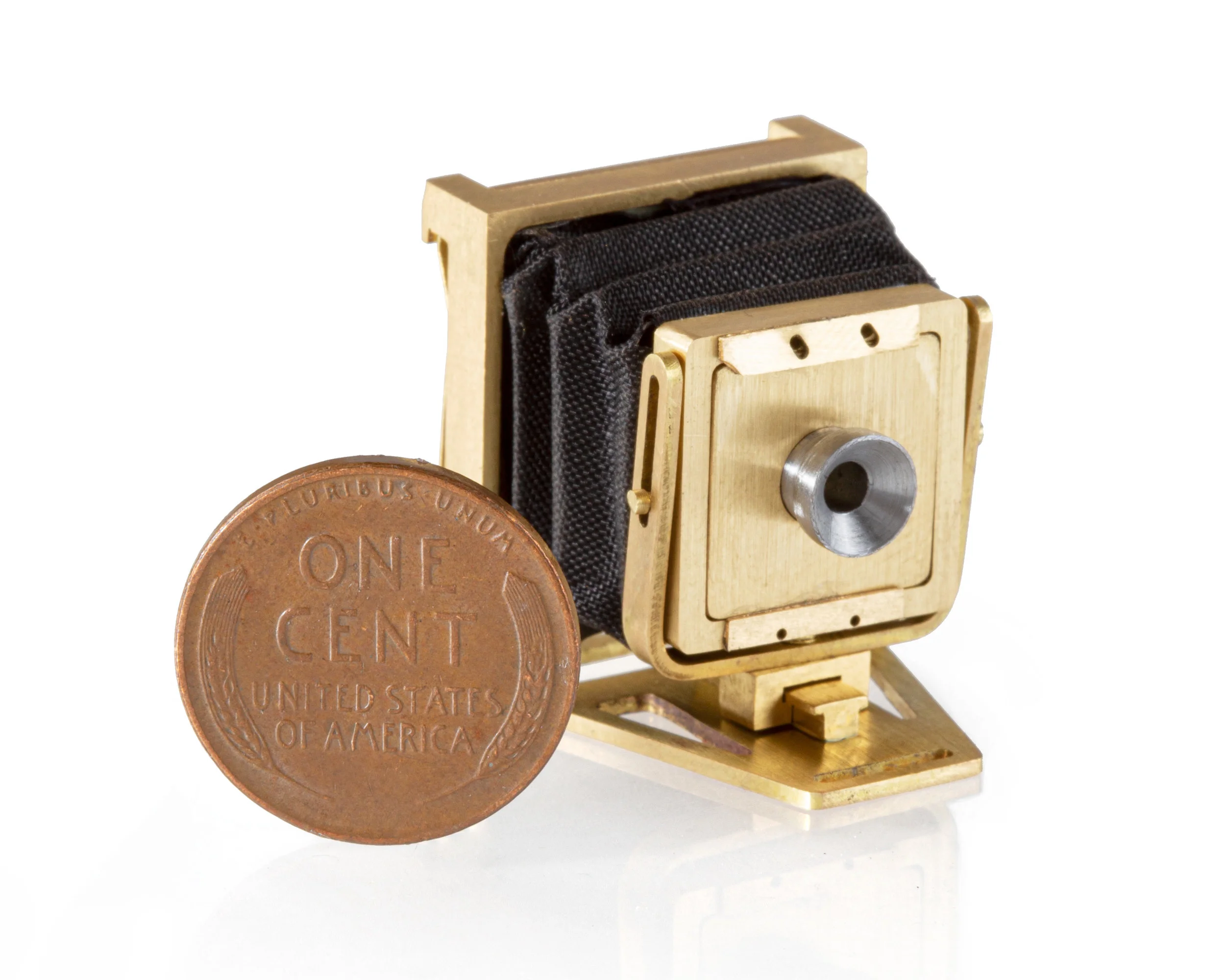


Motivation
The idea for making a miniature view camera came to me about three years ago, but at the time I didnāt yet have the skills required to pull it off so the project was shelved.
After completing the Landers B35, I decided to take a few months off from my normal shop work to focus on some less serious projects and work on some new skills. Then I got an email from the CNC manufacturer Bantam about a contest there were sponsoring. The requirements were simple: Make an object on a CNC machine that fits within a one inch cube and has their red rooster logo incorporated. I instantly knew what to do!
Design
I wanted to go fo a classic large format look, similar to that of Deardorff and other early camera makes. The trick was to simplify the design enough so that it would be possible to manufacture in such a small scale, yet have enough of the features that it still looks as if it could be a full size camera. And as the contest I was entering required that the object be made on a CNC machine, I had to think a lot abut the dimensions of each part so that it could be made with as few operations as possible.
To cut down on the complexity of the design, I went with a method where most of the parts would be cut out a flat sheets of brass, and then bent to shape.
Some of the more complicated parts required multipal opperations on both sides, which would pose a real challenge at this scale.
The Build
The CNC machine used for this build is a Sherline with a home built controller running MACH4.
To make some of the smaller features I have to use end-mills ranging from 1/4in all the way down to 0.5mm. This required the pulleys be upgraded to get the spindle up to 10K RPM.
Even with the increased spindle speed, these tiny end mills proved to be very troublesome!
I designed the components so that several of them could be milled out of a single piece of material at once. Below you can see four parts being machined that will make be used to make the film holder.
A lot of the parts required multiple operations on two or more sides. Below is the front standard, a part requiring machining to be done on four sides. To ensure proper alignment, each cut was measured twice to ensure no mistakes were made.
Bellows
What ended up being the most difficult part was the construction of the bellows. And even now, Iām still looking for ways to improve them.
The main problem lies in finding a material that is very thin and flexible, looks the part, and is still reasonably light tight. What I ended up selecting is a rubberized pneumatic cloth used in the construction of player pianos. This cloth is only 0.004 inches thick and provides an acceptable amount of light protection. However, it is not strong enough to allow the use of this camera in bright areas.





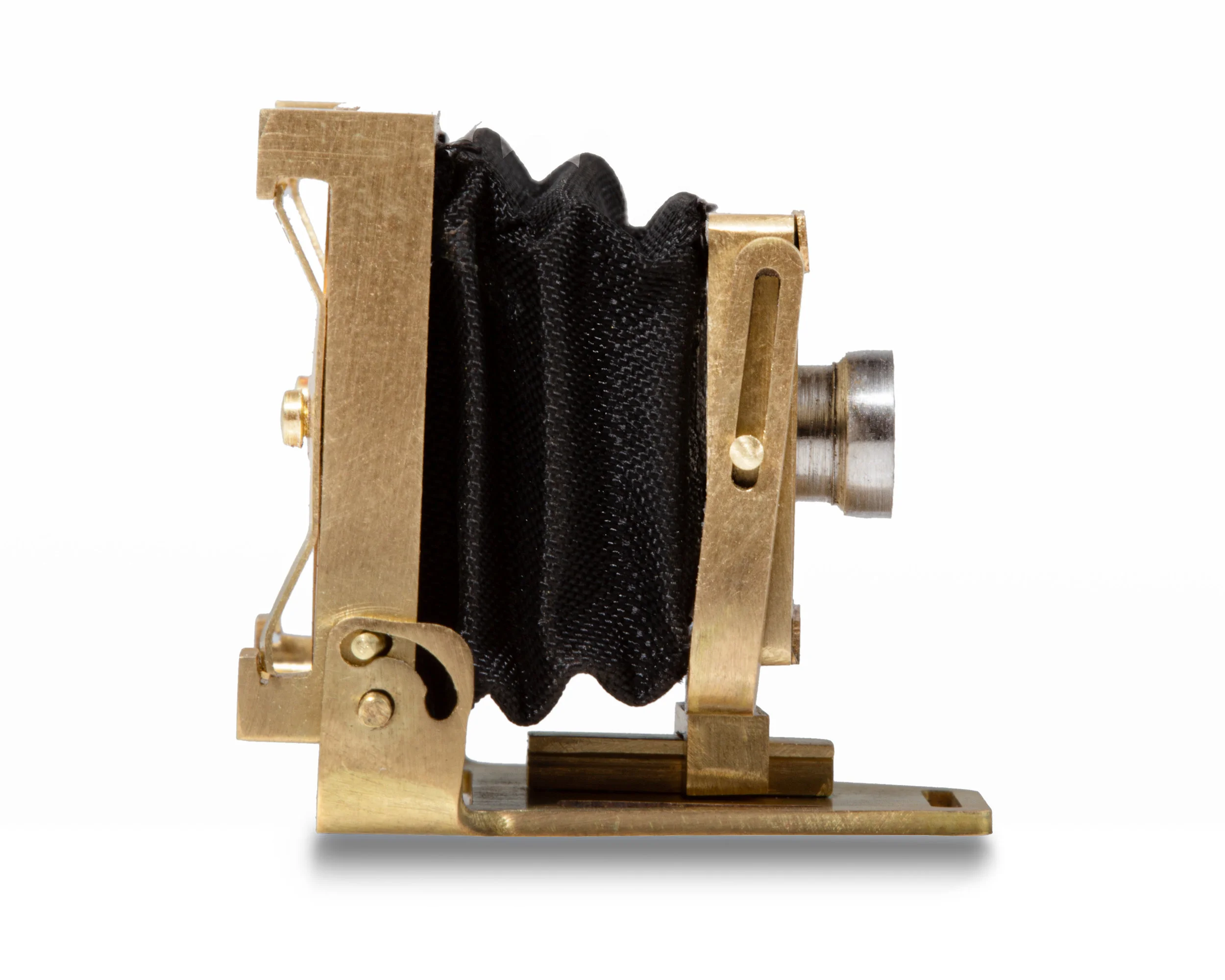
The process starts with a CAD layout made to fit the dimensions of the camera.
The clot and ribs are cut out using these patterns and then clued together. Each fold is then carefully done by hand.
The Negative Holder
Just like with a full size view camera, this camera uses a cut piece of sheet film that is stored inside of a negative holder.
To make this negative holder required milling 5 unique parts. Three parts are sandwiched together to make the actual holder, one is a dark slide, and the final is a plug used to hold the film in and stop light from leaking in.
Shooting with the Worlds Smallest Sheet Film Camera
This camera uses a pinhole lens with an aperture of F90.
Each sheet of film is custom cut from a roll of 35mm film using a 3D printed Jig.
In a completely dark room I cut and load the film into the negative holder. At this point is is safe to turn the lights on but I keep them dim as I want to do everything I can to minimize possible light leaks.
The negative holder slides into the back of the camera. At this point the dark slide can be removed.
The exposure can either be made by removing a lens cap, or in the case of my self portrait, by the use of Strobe lights. The nature of the camera requires a very long exposure time or the use of multiple strobe pops. In my case 20 strobe pops.
The quality of image this camera produces is technically problematic, but aesthetically and creatively very exciting. Overall a real joy to work with and I believe has great potential for very niche applications.
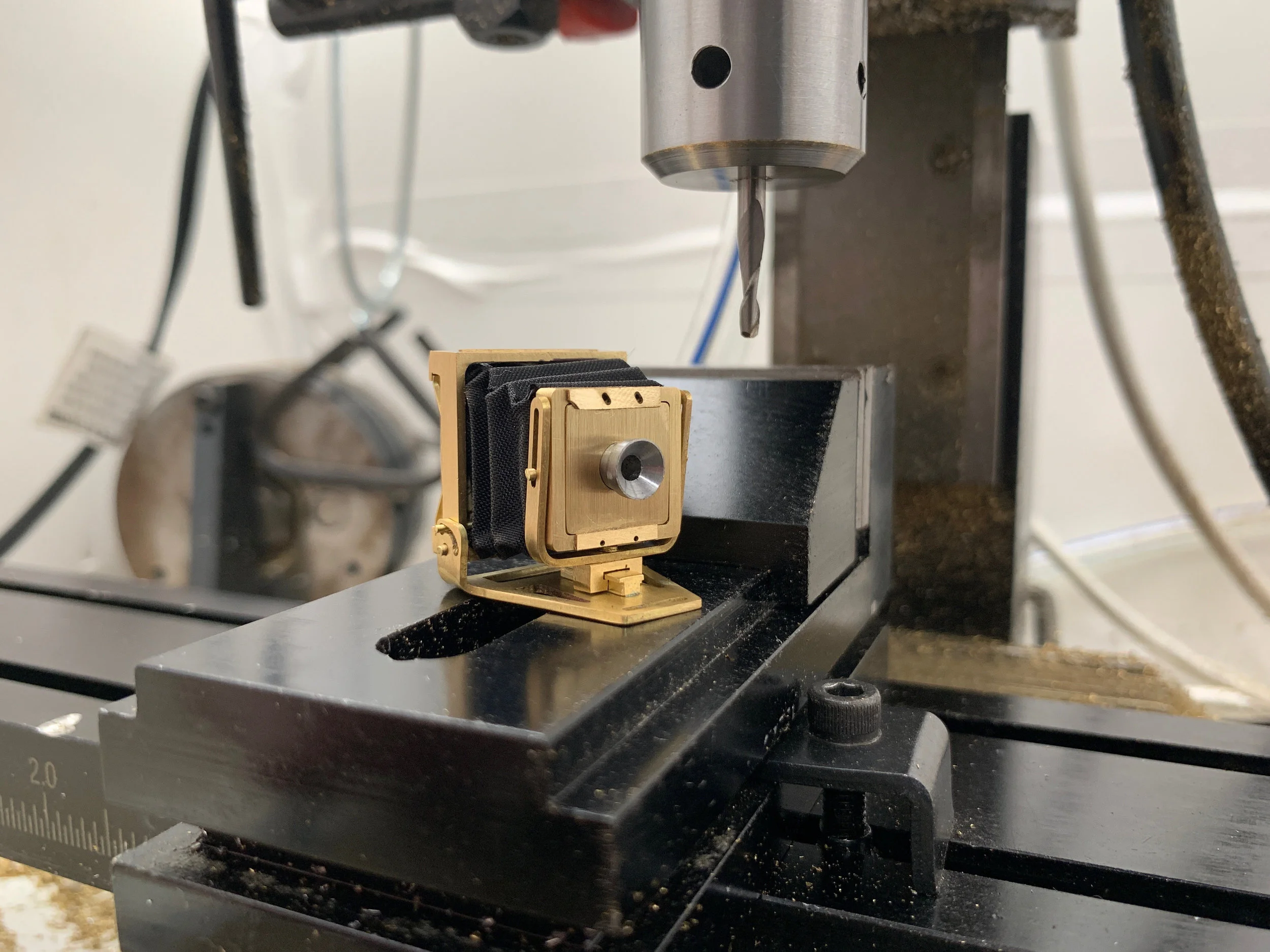
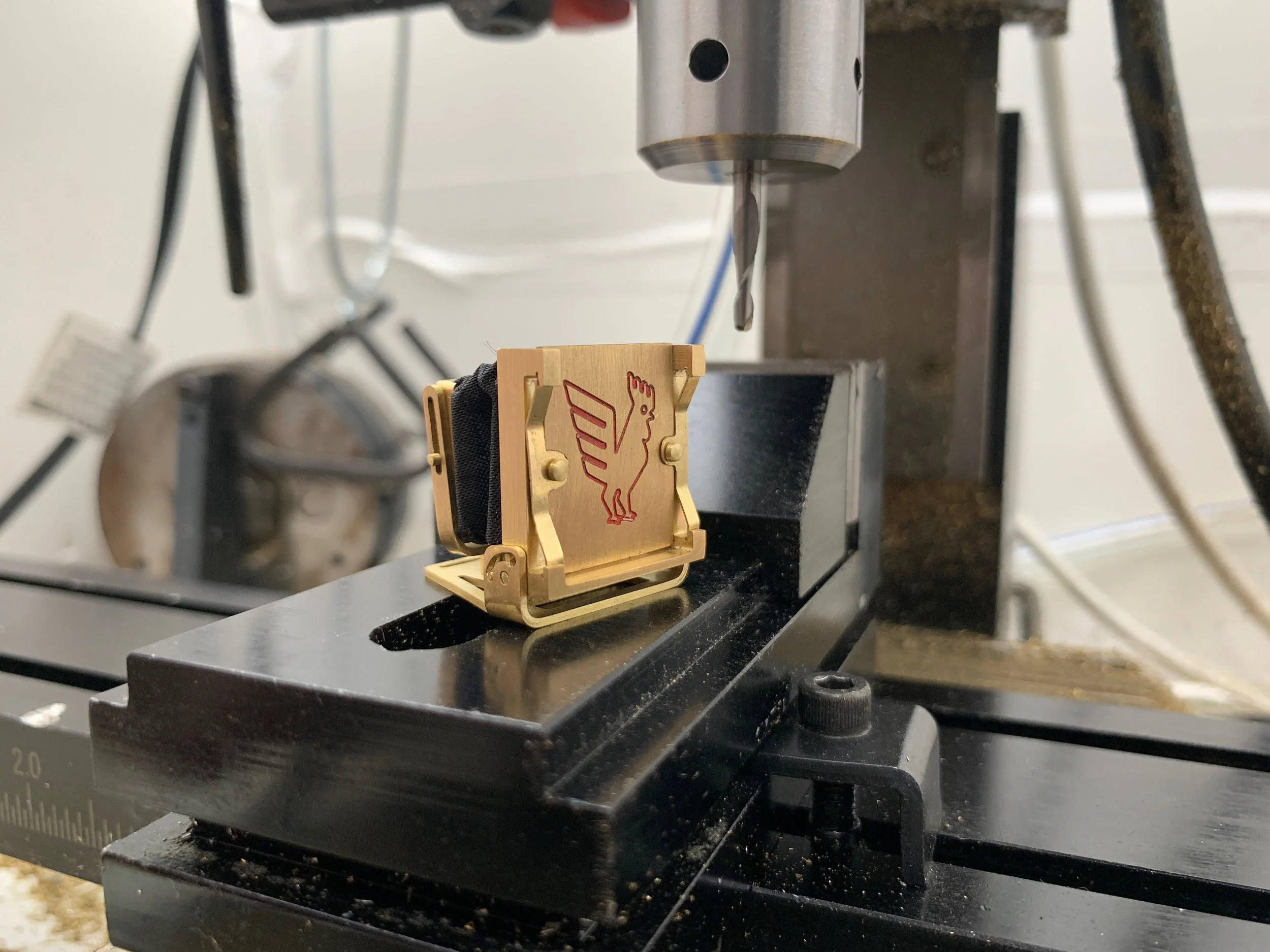
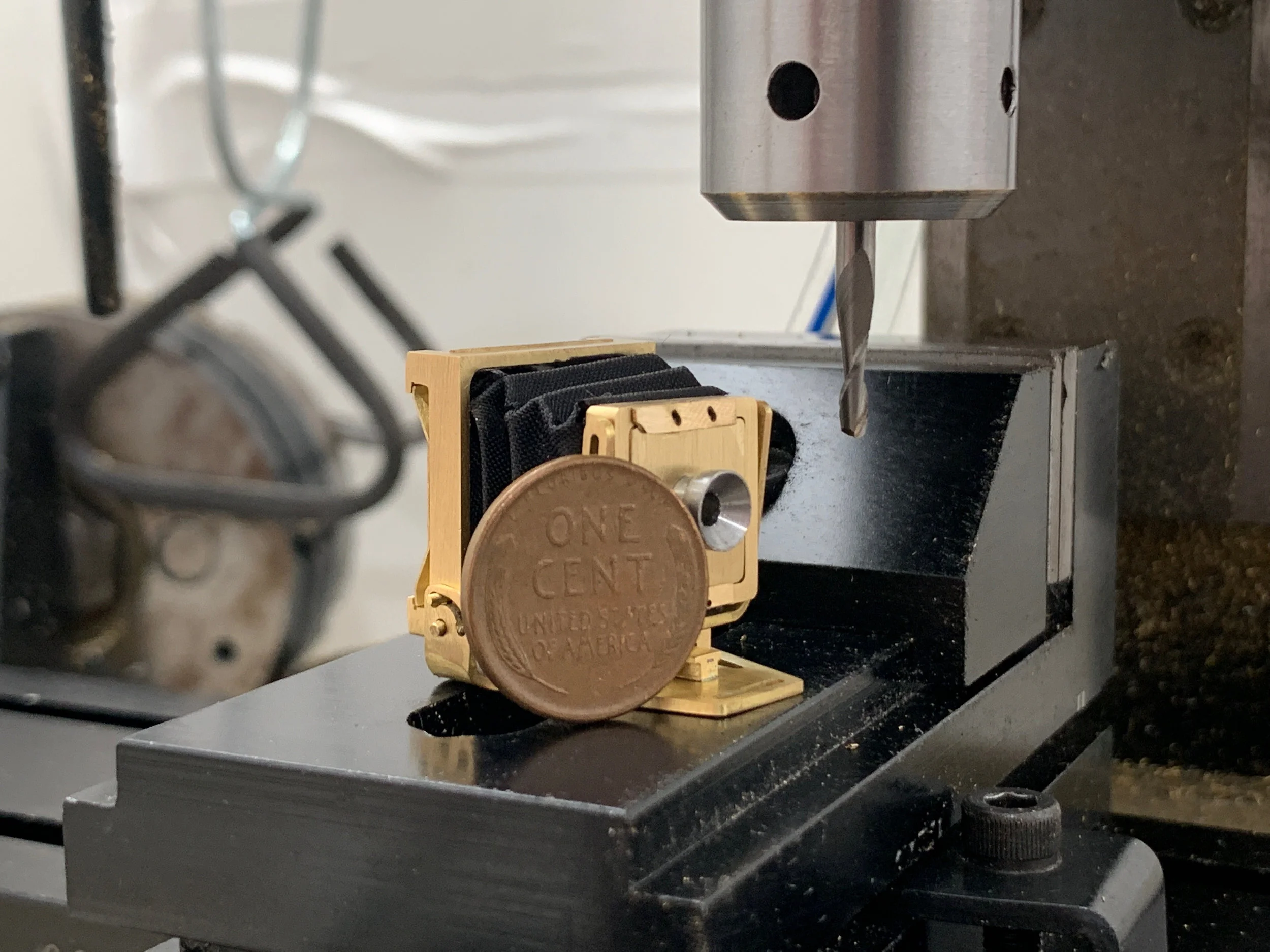