
The pattern for the lens cone next to the completed cone. The pattern is designed on the computer and then 3D printed.
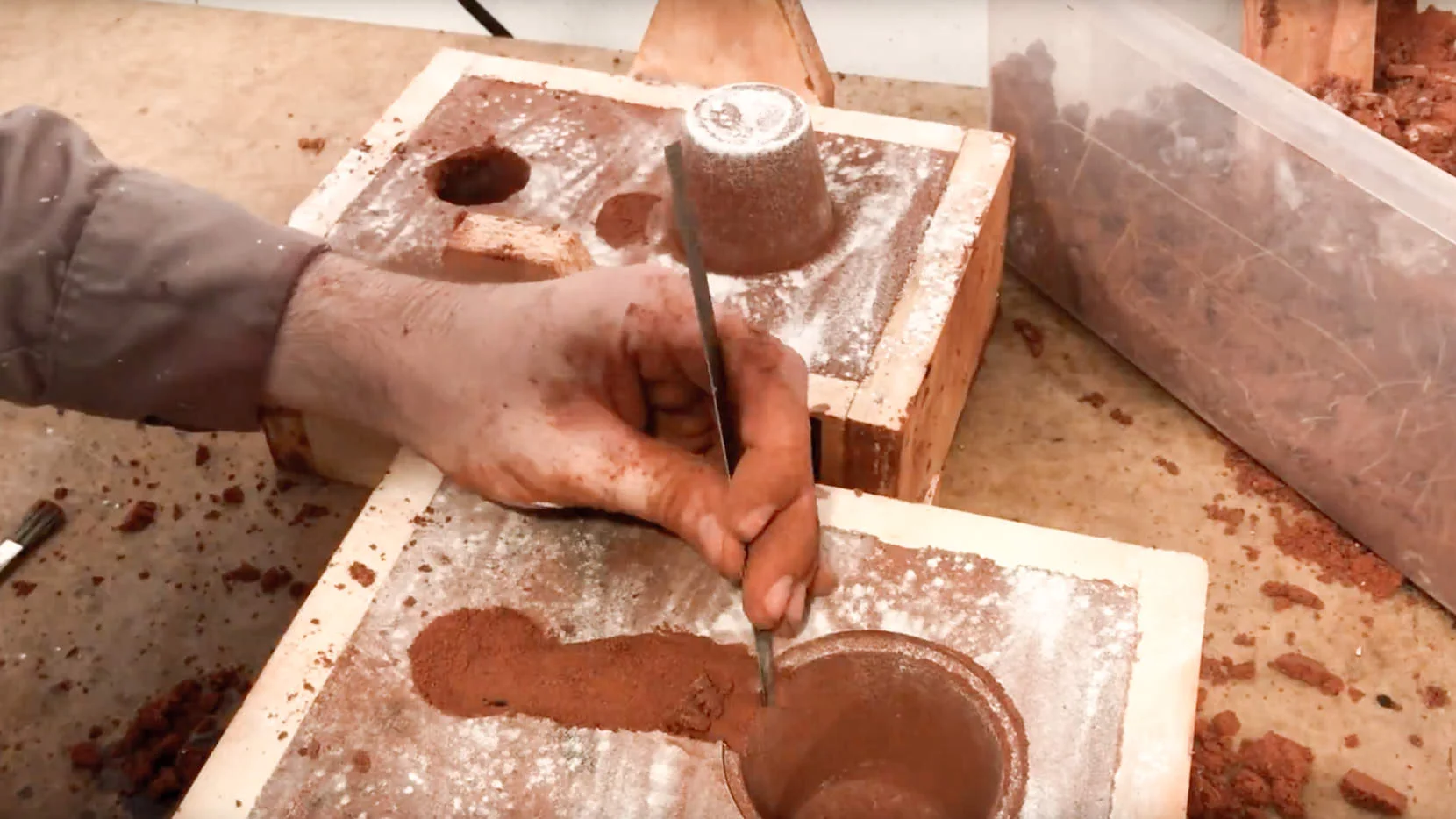
Making the Sand Molds. The red sand you see is Petrobond.

I use an electric kiln to meld down Scrap.
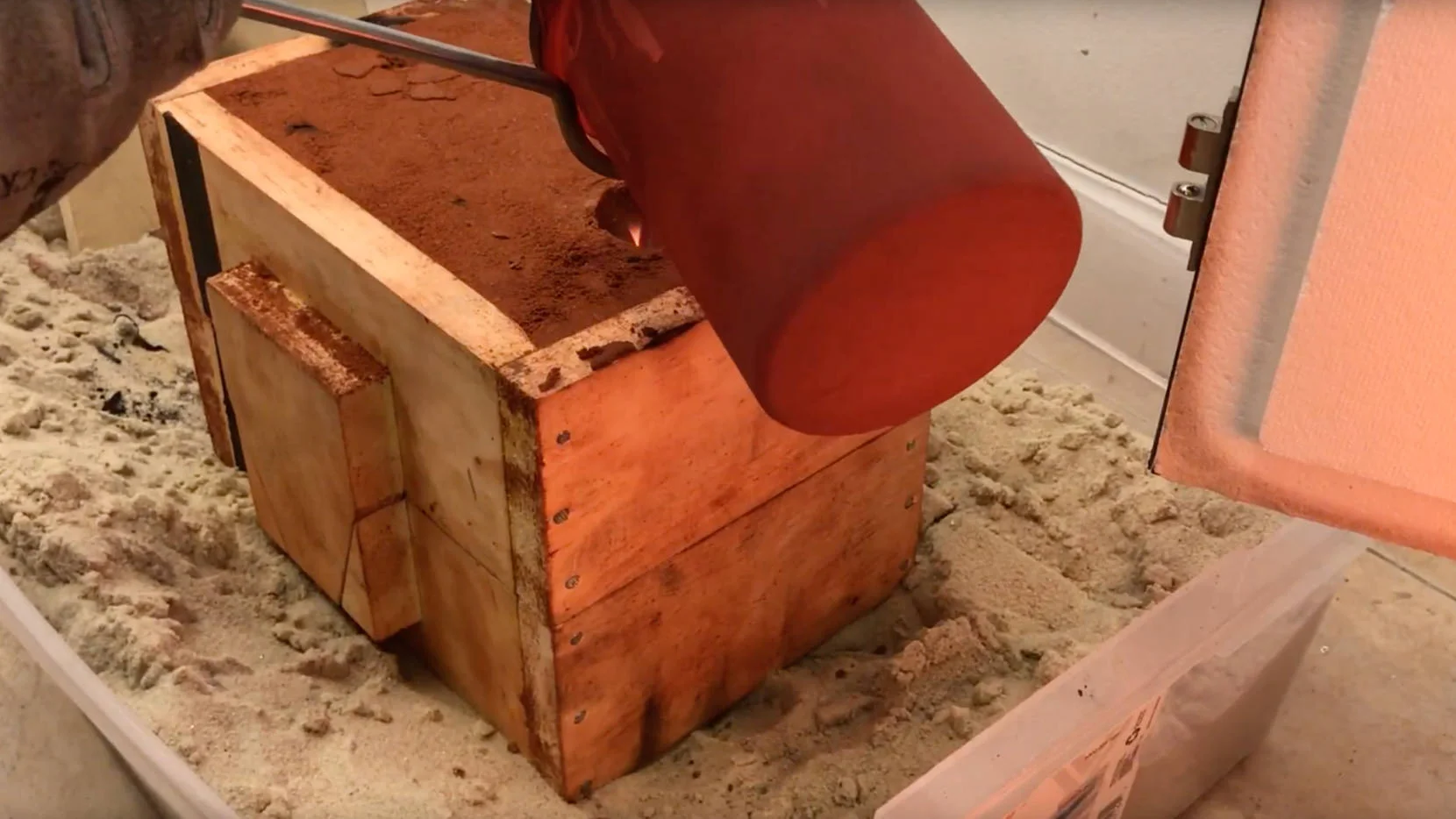
The Melted aluminum is poured into the sand mold previously prepared.

The mold is now left to cool naturally.

A successful pour. It usually takes several tries to get a perfect one.

In its raw state it looks like a mess. Lots of clean up is required.

To speed the process up I'm using a lathe to machine all the external surfaces.

The part is held on the lathe with a superglue arbor so very light passes are made to ensure it doesn’t come off.

Here is is all machined and polished. I'm using a torch to break the super glue that is holding it to the shop made super glue arbor.
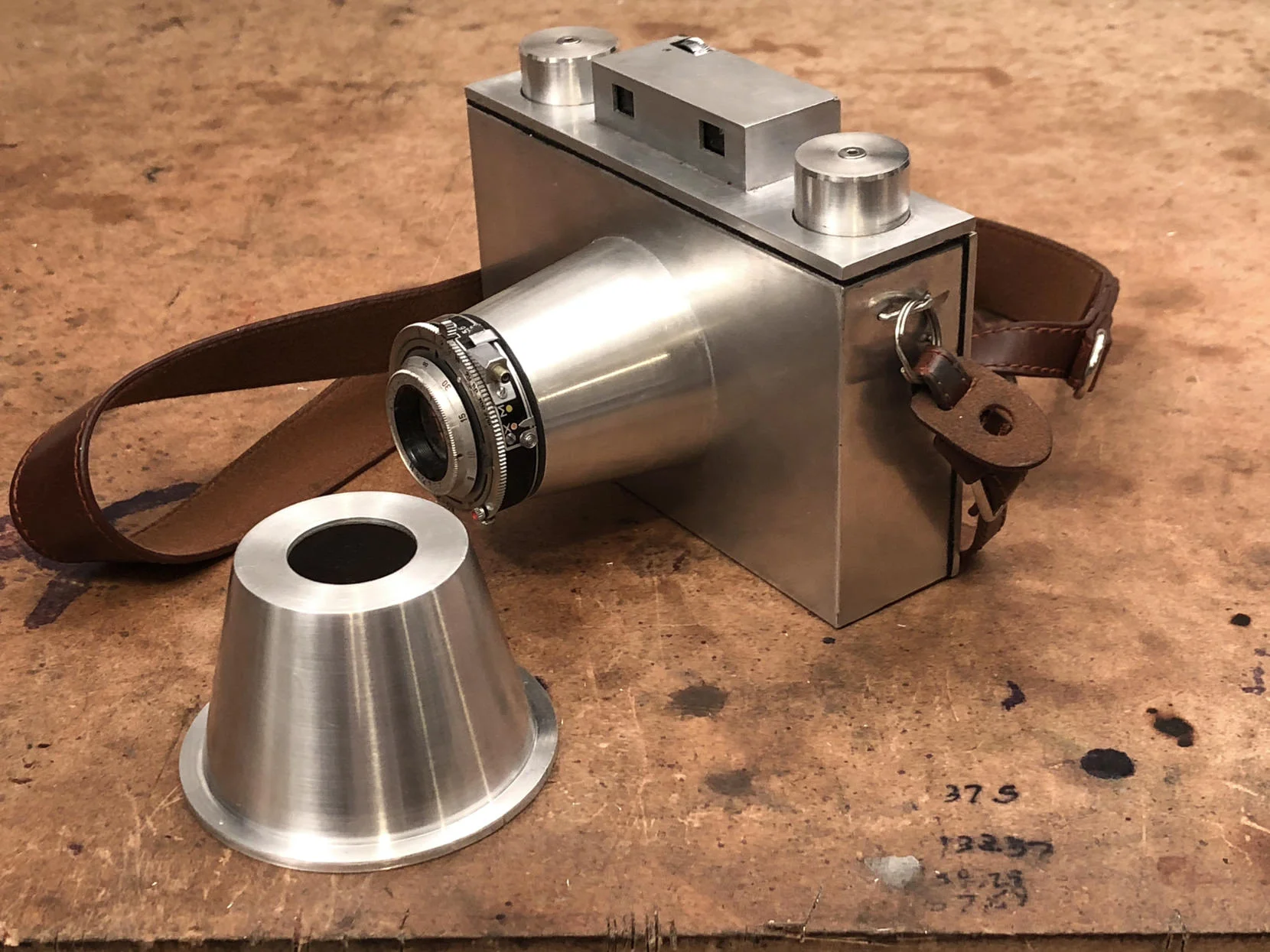
Here is the finished cone next to the previous camera I made.

Here are the parts that make up the main body. They are all cut to size and I use a jig to line them all up.
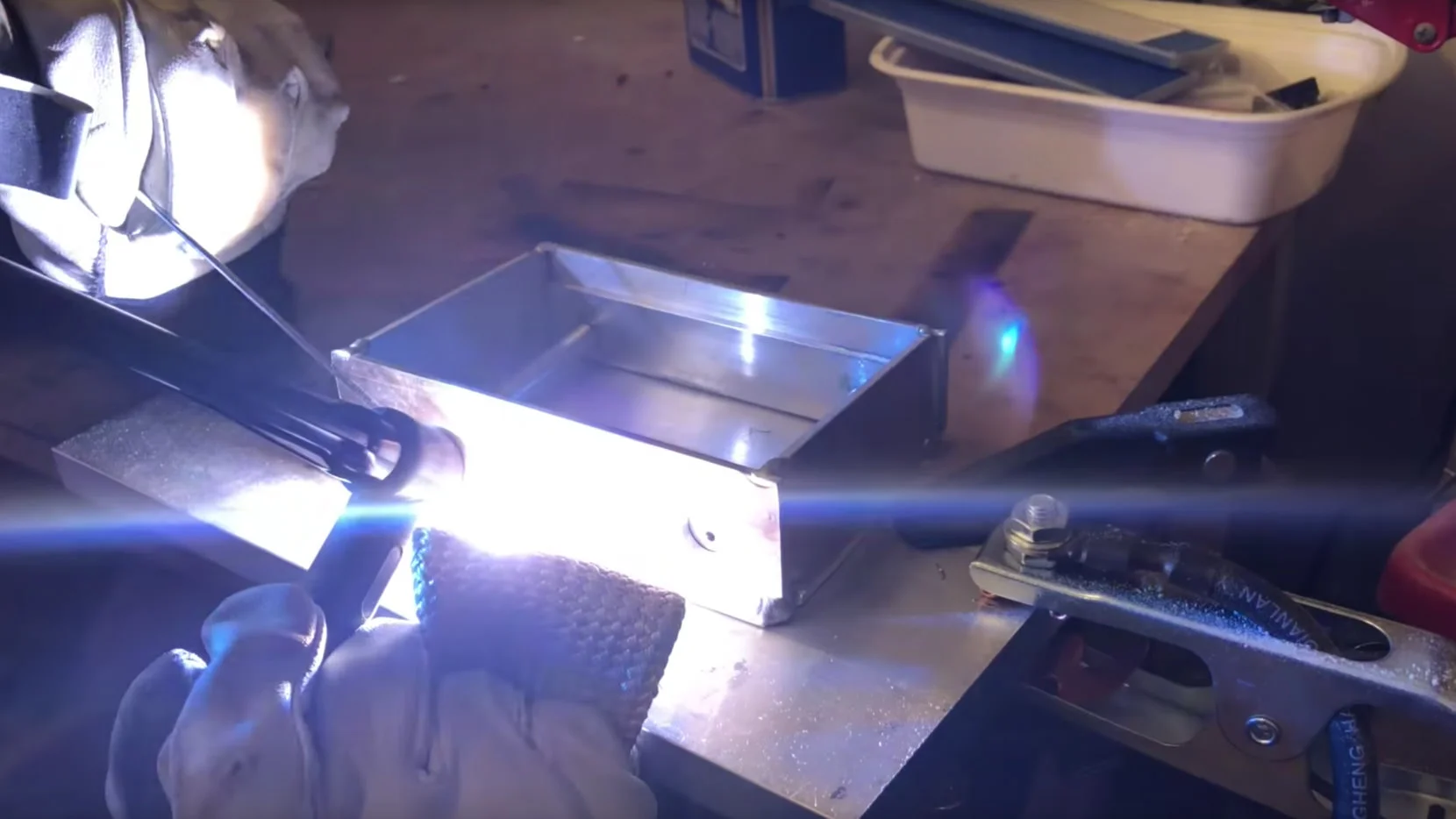
the parts are TIG welded together.
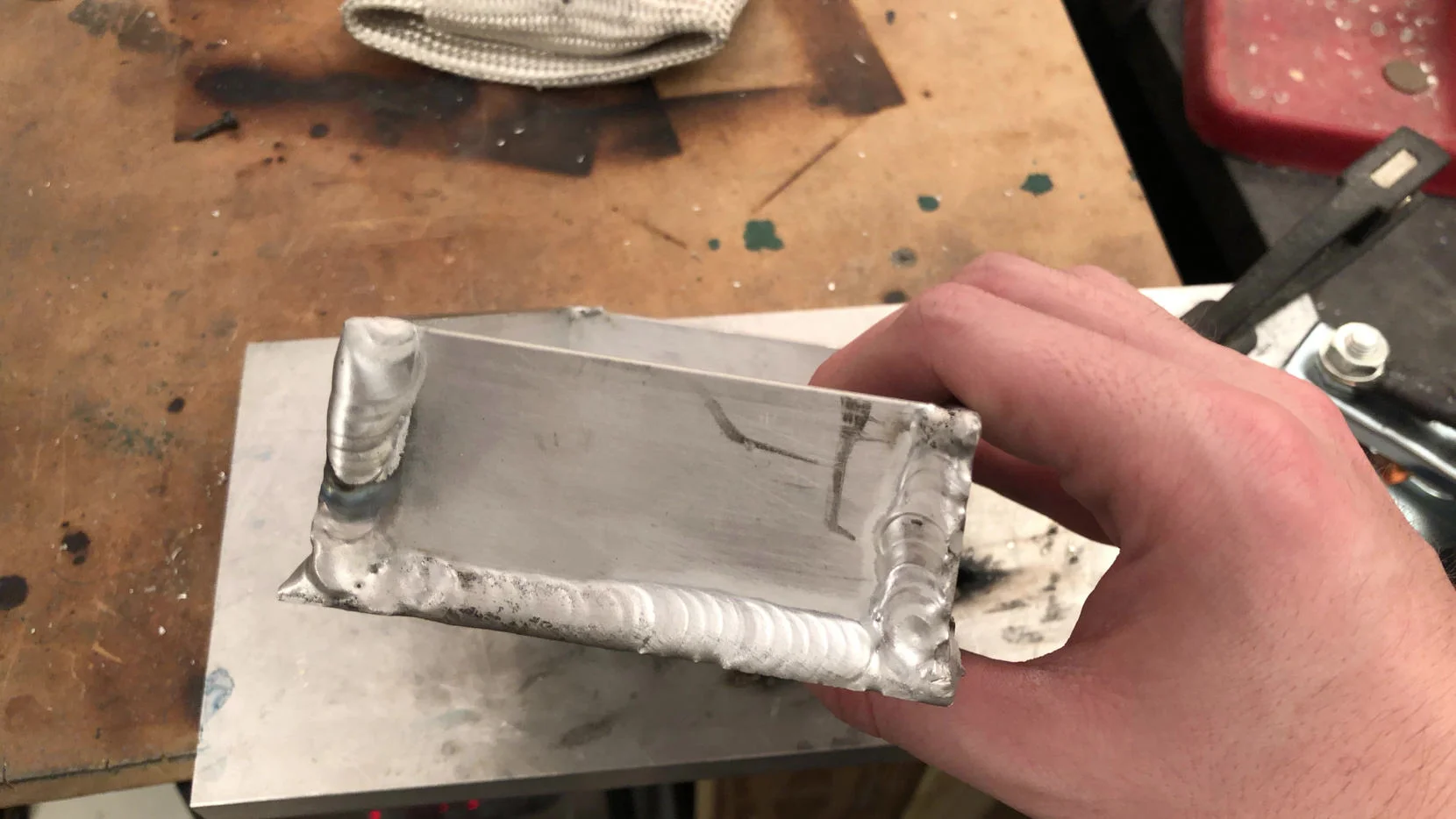
I Actually just started learning how to weld so it looks a little rough.

I use a router with a flush trim bit to lean the welds welds up.
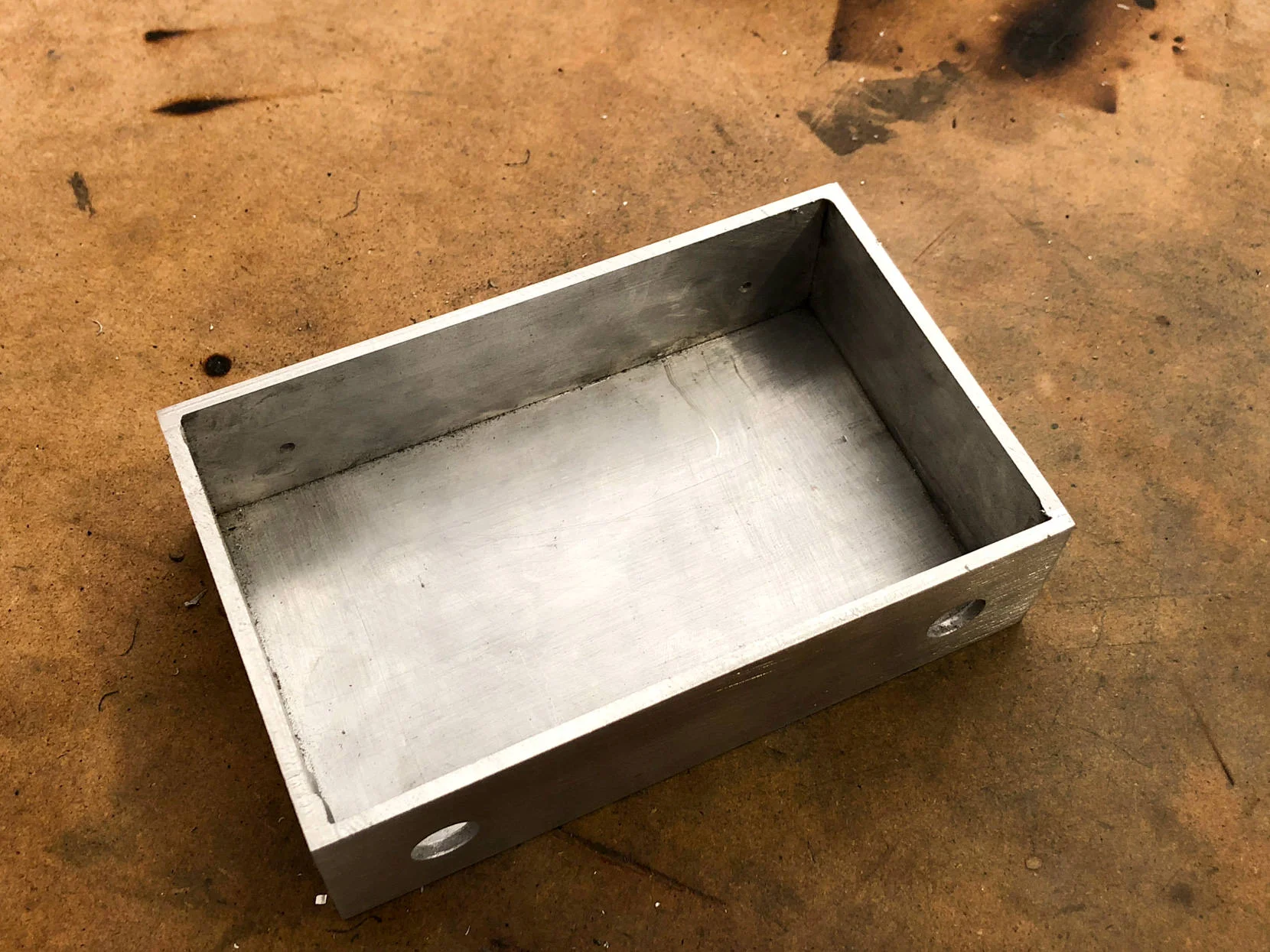
The finished box.
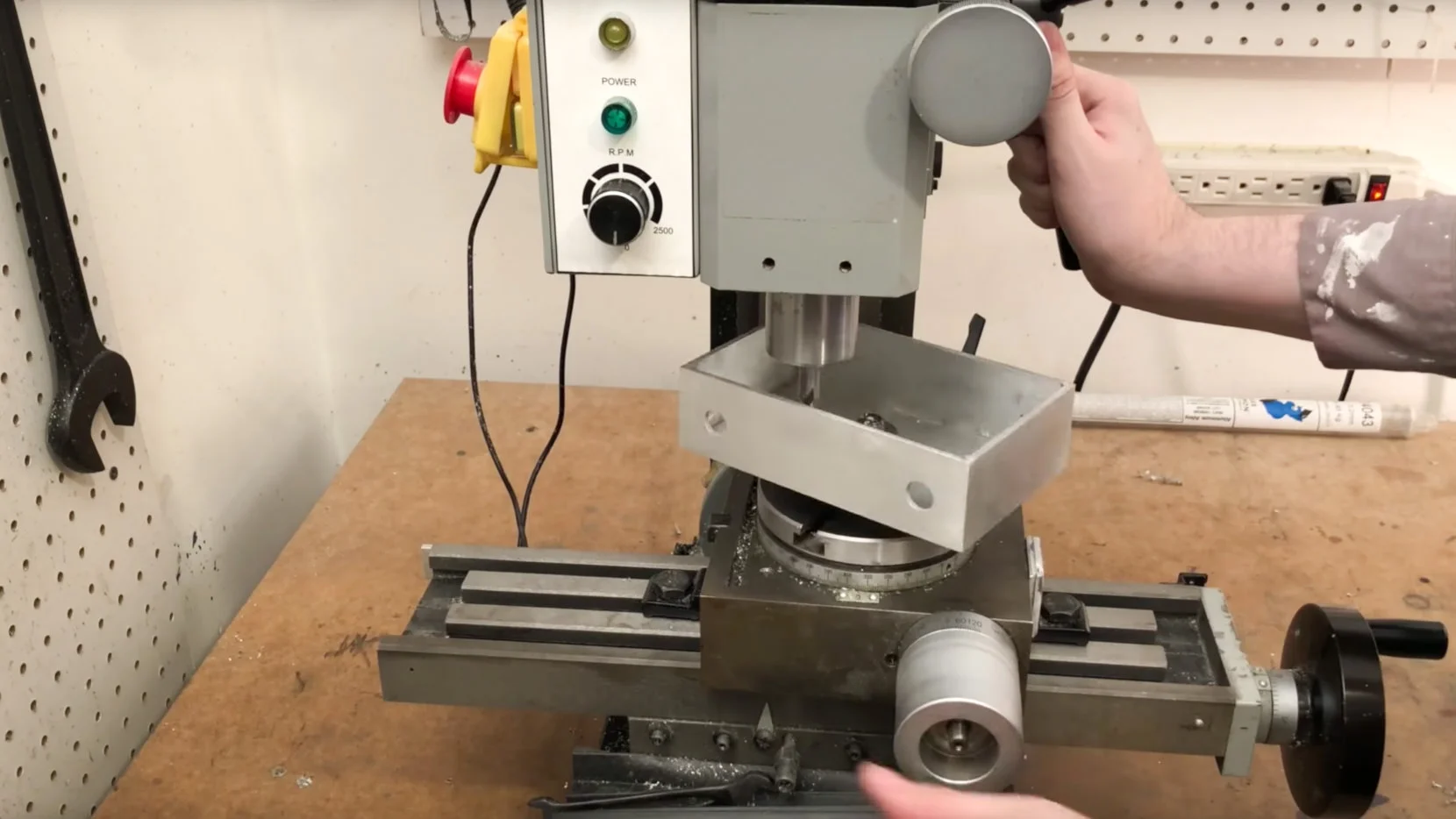
I use a rotary table on my mill to cut a bit hole in the middle.

The nose cone will be inserted into this hole.

The cone is a press fit in the hole. Nothing but friction. I heat the body up to make it expand slightly and I freeze the cone to make it shrink a bit. when they are but together they temperature equalizes and they become permanently bonded.

Next is the top cap. Once again the pattern is design and printed and a mold is made to cast in aluminum

Here are the sand molds

The cast wasn't perfect but I used my new found tig welding skills to repair small defects.

The Outside is completely machined on the mill.

All features are marked out.

Two holes are cut to accept the film advance knobs that I'll make later.

A small end mill is used to cut out the viewing windows.

Here is the top cap on the main body.

This is the range finder that will be installed in the top cap in the end of the project.

This part will become the tripod mount. A 1/4-20 thread will be added to the center and the edges rounded.

Here it is in a near complete state.

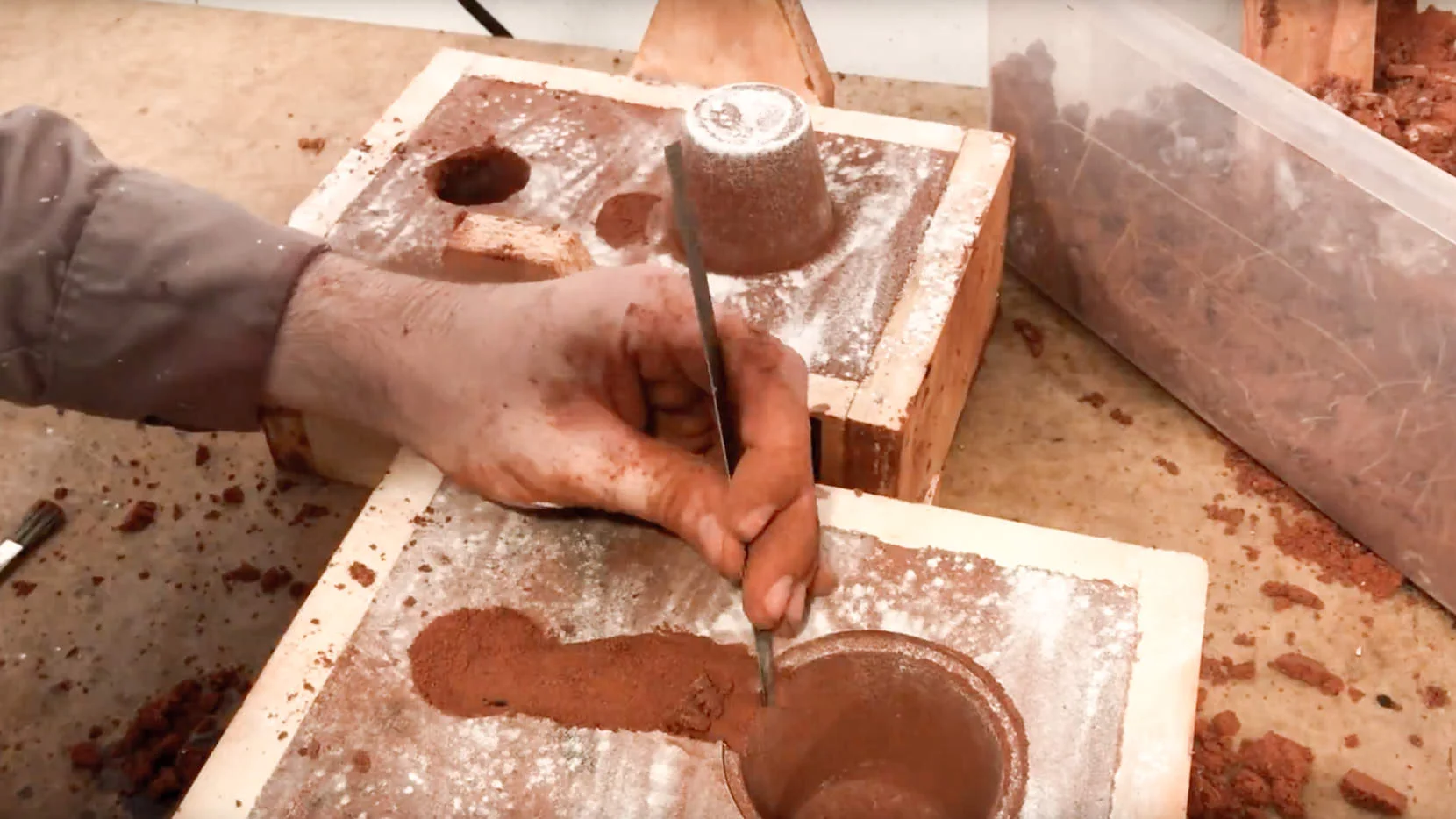

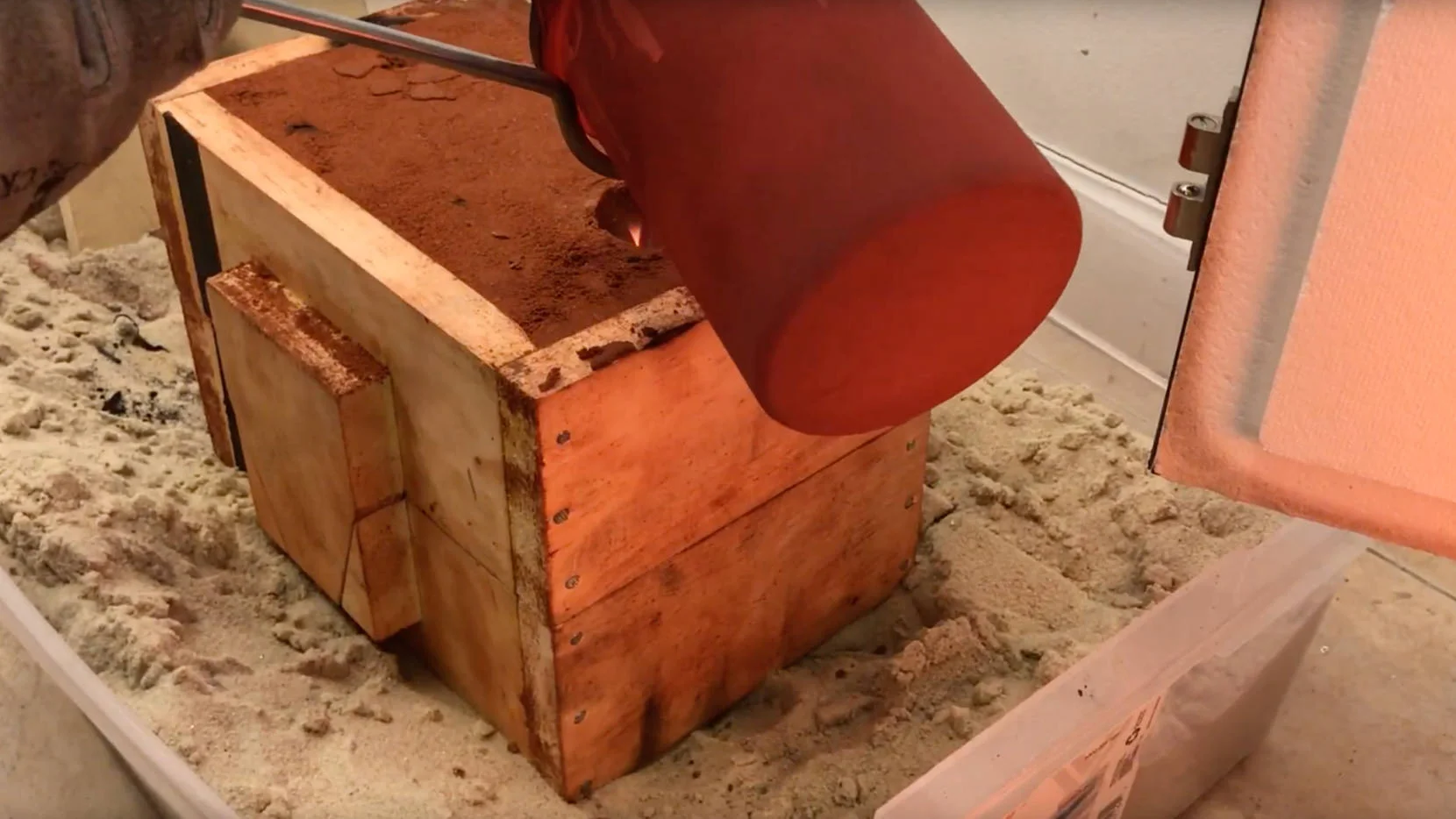






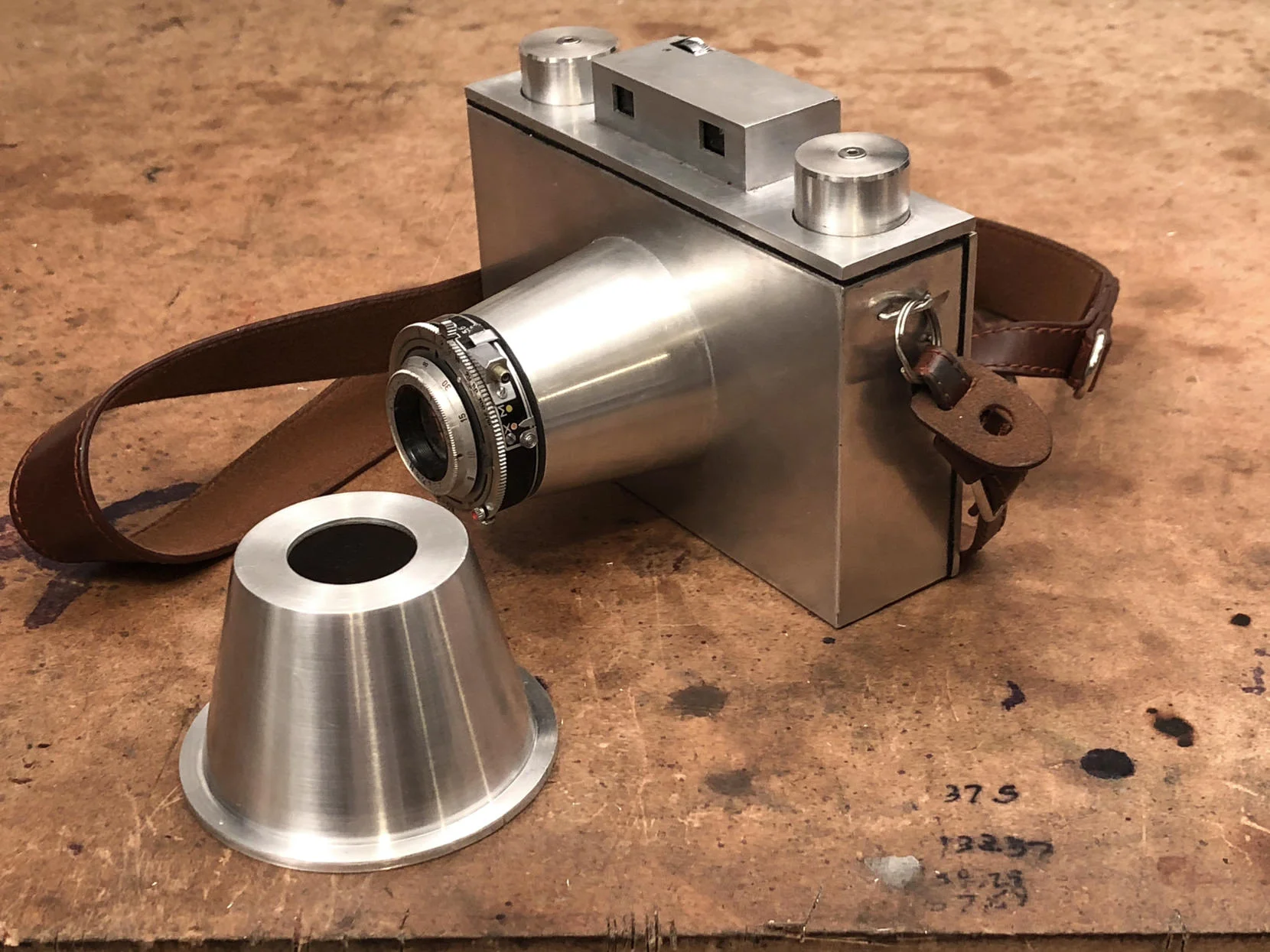

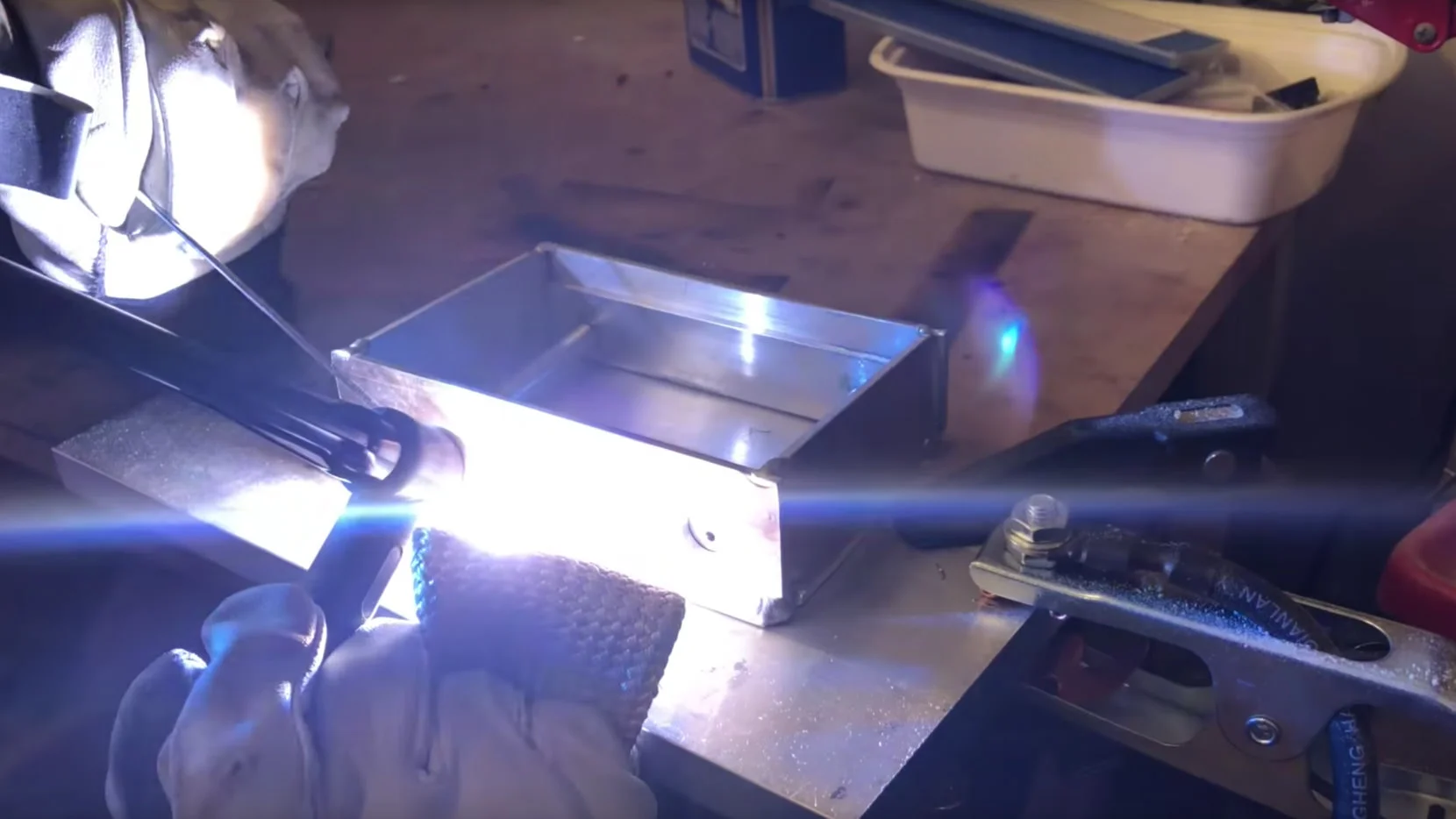
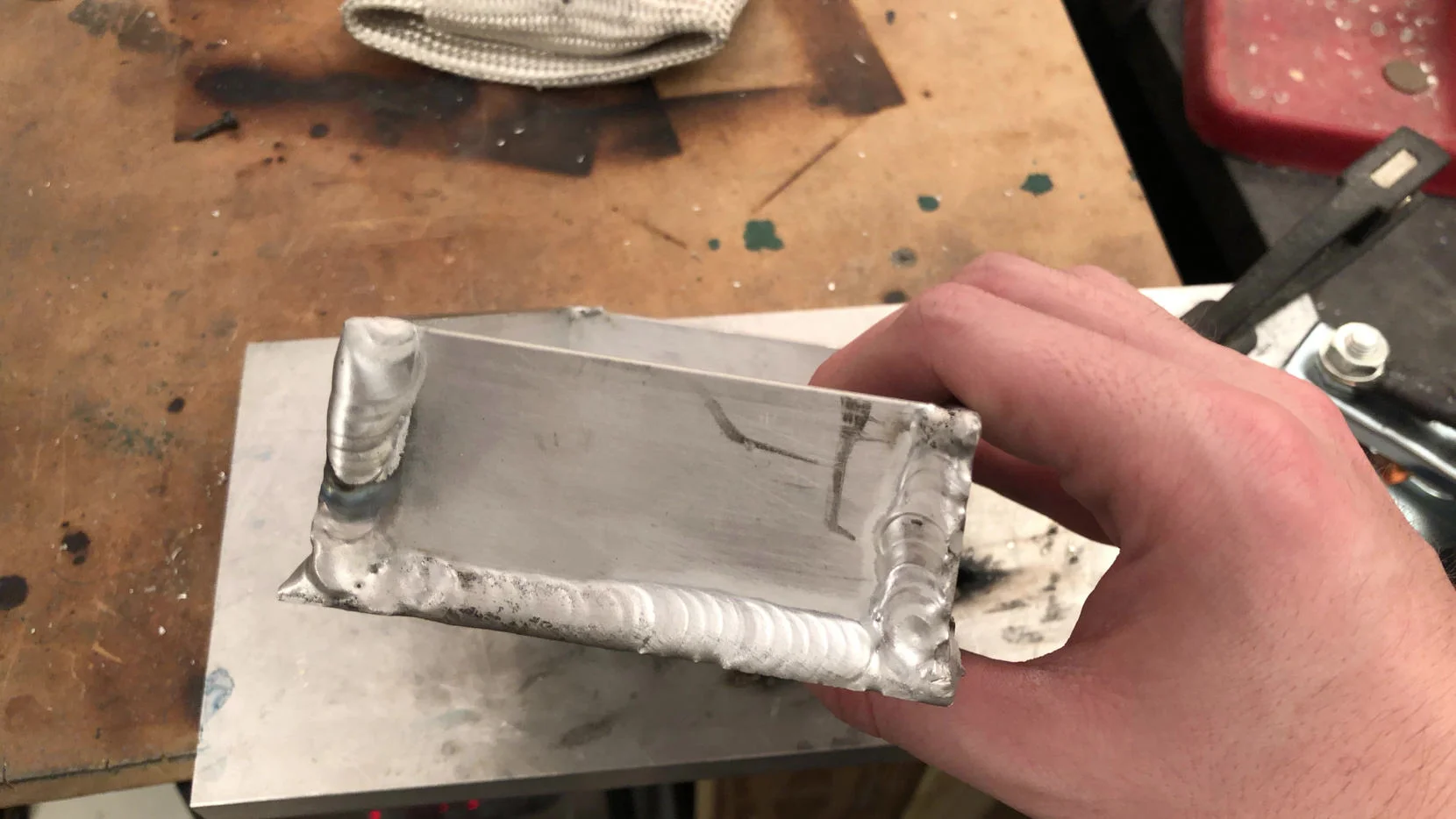

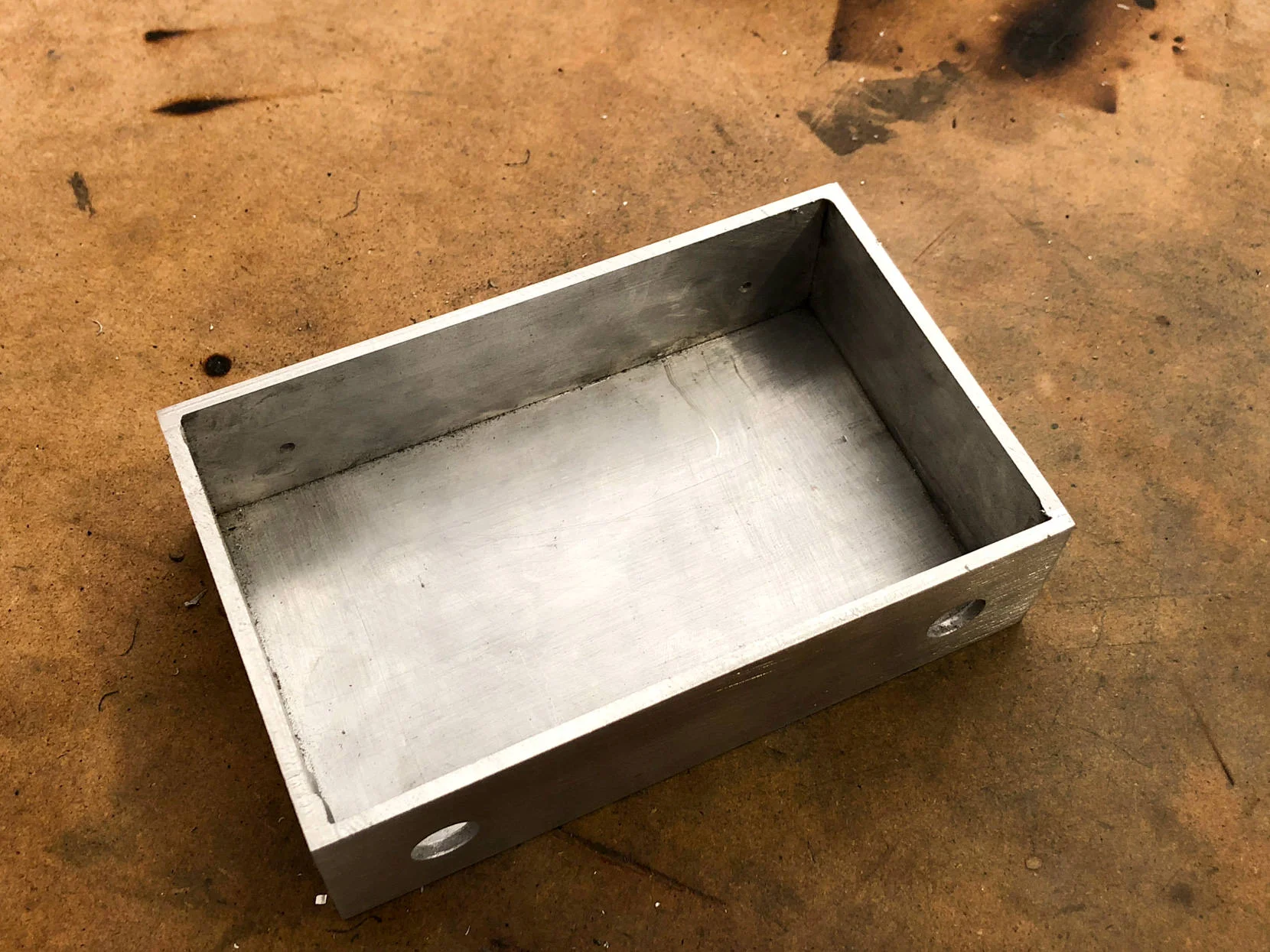
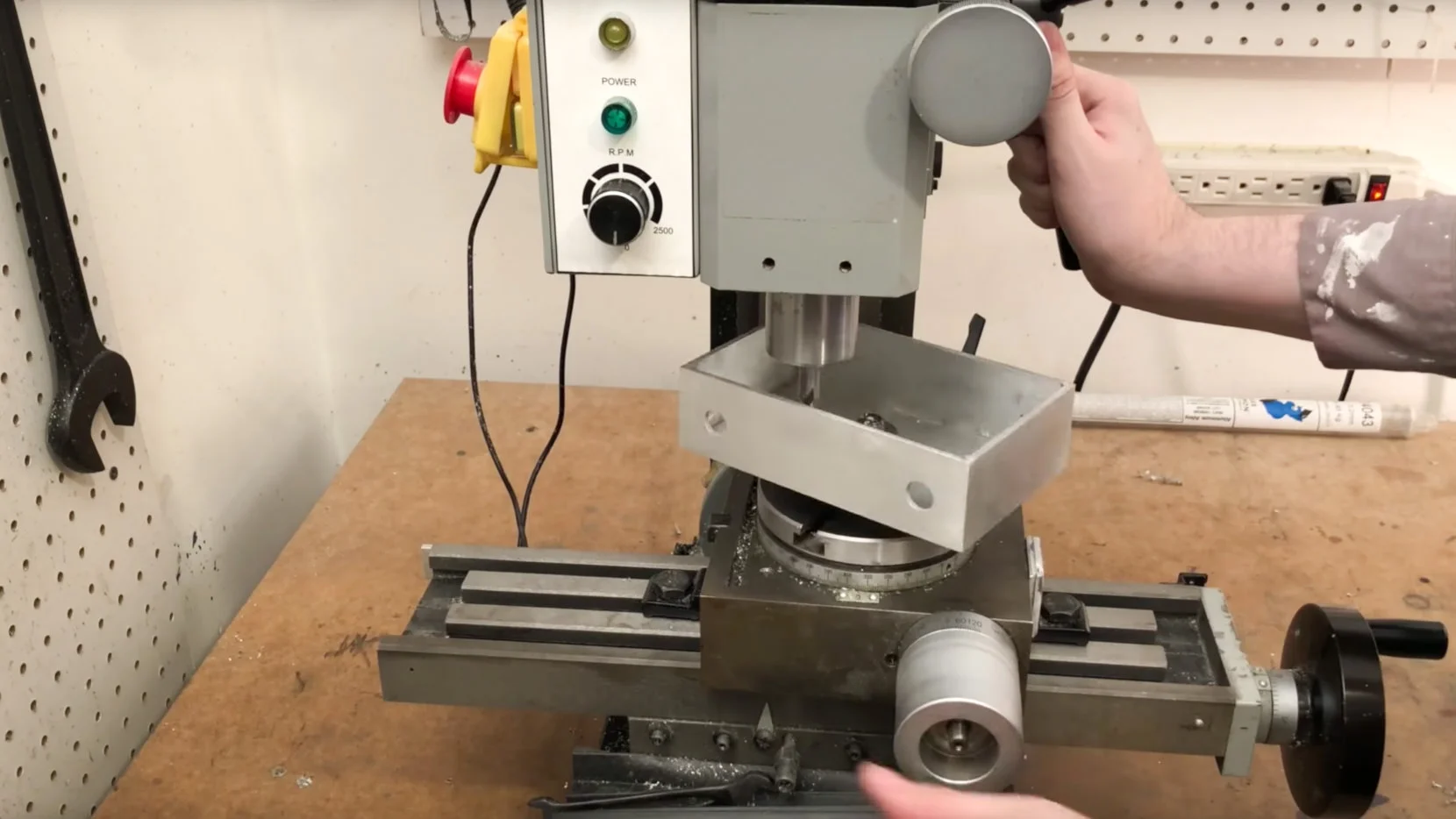













The pattern for the lens cone next to the completed cone. The pattern is designed on the computer and then 3D printed.
Making the Sand Molds. The red sand you see is Petrobond.
I use an electric kiln to meld down Scrap.
The Melted aluminum is poured into the sand mold previously prepared.
The mold is now left to cool naturally.
A successful pour. It usually takes several tries to get a perfect one.
In its raw state it looks like a mess. Lots of clean up is required.
To speed the process up I'm using a lathe to machine all the external surfaces.
The part is held on the lathe with a superglue arbor so very light passes are made to ensure it doesn’t come off.
Here is is all machined and polished. I'm using a torch to break the super glue that is holding it to the shop made super glue arbor.
Here is the finished cone next to the previous camera I made.
Here are the parts that make up the main body. They are all cut to size and I use a jig to line them all up.
the parts are TIG welded together.
I Actually just started learning how to weld so it looks a little rough.
I use a router with a flush trim bit to lean the welds welds up.
The finished box.
I use a rotary table on my mill to cut a bit hole in the middle.
The nose cone will be inserted into this hole.
The cone is a press fit in the hole. Nothing but friction. I heat the body up to make it expand slightly and I freeze the cone to make it shrink a bit. when they are but together they temperature equalizes and they become permanently bonded.
Next is the top cap. Once again the pattern is design and printed and a mold is made to cast in aluminum
Here are the sand molds
The cast wasn't perfect but I used my new found tig welding skills to repair small defects.
The Outside is completely machined on the mill.
All features are marked out.
Two holes are cut to accept the film advance knobs that I'll make later.
A small end mill is used to cut out the viewing windows.
Here is the top cap on the main body.
This is the range finder that will be installed in the top cap in the end of the project.
This part will become the tripod mount. A 1/4-20 thread will be added to the center and the edges rounded.
Here it is in a near complete state.